Comment optimiser les propriétés mécaniques de pièces imprimées en FDM grâce au Machine Learning ?
Les industriels visent aujourd’hui à utiliser la fabrication additive pour des applications fonctionnelles structurales. Cela nécessite une mise en œuvre optimale. Toutefois, les procédés de fabrication additive se caractérisent par un nombre important de paramètres matériau et procédé. L’identification des optimums peut donc s’avérer longue et coûteuse avec les approches traditionnelles d’analyse de données. INOVSYS a validé expérimentalement la pertinence des outils de Machine Learning appliqués à l’impression 3D FDM.
INOVSYS, plateforme dédiée à la validation et au transfert de technologies mécaniques, a développé une expertise dans la prise en main des matériaux hautes performances par procédé FDM, parmi lesquels se trouvent les thermoplastiques de la famille des PAEK (poly aryl éther cétones). Cet ensemble regroupe des polymères tels que le PEEK, le PEKK ou encore le PEI, tous étant reconnus pour leur excellentes propriétés mécaniques. Découvrez notre précédent article ici sur la prise en mains d’un nouveau matériau.
Afin d’optimiser le traitement des données issues des essais de caractérisation des propriétés mécaniques, INOVSYS a choisi d’implémenter dans son processus un puissant outil d’analyse : Le Machine Learning.
Par un procédé d’apprentissage s’appuyant sur des approches statistiques, le logiciel conçoit un modèle mathématique basé sur les données des essais. L’ordinateur acquiert par ce biais la capacité à « apprendre » à partir des données, ouvrant ainsi la porte à l’optimisation et la prédiction paramétrique.
Cet article est consacré aux récents travaux d’INOVSYS sur l’optimisation des paramètres machines pour l’amélioration des propriétés mécaniques en statique du PEKK-A (Kimya).
1. Les enjeux industriels des matériaux FDM hautes performances
Les procédés de fabrication additive sont vecteurs d’innovation. Ils apportent une nouvelle manière de penser la pièce mécanique en permettant une grande liberté géométrique et la possibilité de s’affranchir des outillages. Ils décuplent le champ des possibles par l’optimisation topologique et la formulation de matériaux imprimables toujours plus performants. Enfin, ils laissent entrevoir de nombreuses voies de progrès. De grands groupes tels que Airbus, Safran, ou encore ORANO entrevoient le potentiel de cette technologie en tant que réponse aux enjeux industriels de demain.
Mis en œuvre dans des conditions optimales, le PEKK (Poly Ether Cétone Cétone) fait figure de réponse à cette problématique industrielle. Ce matériau dispose en effet de propriétés hors normes : légèreté, résistance en continue à des températures très élevées et aux agents chimiques, tenue à l’abrasion. A cela s’ajoutent ses excellentes propriétés mécaniques en statique qui, une fois renforcés par l’ajout de fibres, lui confère une résistance comparable à certains métaux.
Couplé au procédé FDM, il devient alors possible de réaliser des pièces affichant un rapport poids/résistance qui s’avère particulièrement intéressant dans le cadre de remplacements de pièces métalliques existantes.
Les similarités microstructurales du PEKK avec les autres matériaux de la famille des PAEK donnent à cette étude un caractère transverse.
Le PEEK, par sa nature de matériau semi-cristallin, est un polymère également très prisé dans les domaines industriels qui nécessitent la réalisation de pièces offrant à la fois d’excellentes propriétés mécaniques et un rapport poids/résistance optimal. Le caractère biocompatible du PEEK en fait de plus un excellent candidat pour la réalisation d’implants dans le domaine médical.
2. Sélection des paramètres machines FDM les plus influents
Le procédé FDM compte un nombre important de paramètres machines. Le nombre auquel l’opérateur a accès varie en fonction du logiciel de slicing utilisé. Cependant, parmi les dizaines de paramètres modifiables, une poignée seulement ont un impact significatif sur les propriétés mécaniques de la pièce finie.
Afin de sélectionner les plus influents, INOVSYS a réalisé un travail de bibliographie en analysant la littérature scientifique. Le résultat : huit paramètres sortent du lot lorsque l’on cherche à optimiser la résistance à la rupture en traction et le module d’élasticité. Afin de faciliter la réalisation des premiers essais et de limiter le nombre d’éprouvettes à imprimer, ces paramètres ont été scindés en deux groupes de quatre.
Un premier groupe est composé de la température d’impression, de la hauteur de couche, de la vitesse d’impression et du taux de remplissage. Ils sont évalués sur trois niveaux de variation.
Un second groupe de paramètres comporte l’angle de dépose, la largeur d’extrusion au remplissage, le chevauchement des cordons au remplissage et le nombre de contours.
Mis à part leurs impacts respectifs sur différents aspects de la pièce finale, les huit paramètres sélectionnés dans le cadre de ces travaux ont tous un point commun : leur influence non négligeable sur le taux de porosités. En effet, l’inclusion d’air au sein d’une pièce fabriquée par procédé FDM est une problématique bien connue. Sous l’effet d’une contrainte mécanique de traction, chaque interstice généré lors de la dépose peut jouer le rôle d’amorce de fissure provoquant une rupture prématurée de l’éprouvette. Un taux de porosités très faible est donc primordial afin d’obtenir de bonnes propriétés mécaniques.
3. Construction du plan d’expérience pour les éprouvettes imprimées
Le choix de la norme d’essai utilisée pour la réalisation des éprouvettes a été fait sur la base de deux éléments :
- Le risque de rupture dans les congés de l’éprouvette
- La communication sur les résultats obtenus et leur comparaison avec des valeurs existantes.
En suivant ces directives, la norme ASTM D-638 a été retenue pour sa polyvalence et la géométrie des éprouvettes comportant de larges rayons de courbure, facteur primordial lorsque l’on envisage la comparaison avec des thermoplastiques renforcés (limitation du risque de rupture dans les congés).
Le plan d’expérience a été défini afin d’optimiser le nombre d’éprouvettes à imprimer en fonction des paramètres à observer, tout en conservant une approche statistique pertinente. INOVSYS a fait le choix d’utiliser les tables de Taguchi pour structurer son mode opératoire.
Les tables de Taguchi permettent la constitution de plans d’expérience ayant l’avantage de diminuer de manière considérable le nombre d’essais à réaliser pour l’observation de l’influence d’un grand nombre de paramètres.
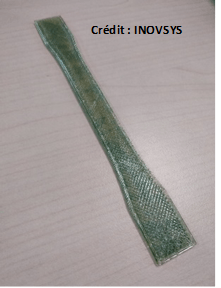
4. L’apport du machine learning dans l’optimisation des propriétés mécaniques des pièces imprimées
Afin de traiter les données issues des essais mécaniques, INOVSYS a choisi le logiciel d’apprentissage KNIME qui présente notamment l’avantage d’être open source.
Nous avons tout d’abord visualisé les courbes liant propriétés mécaniques et paramètres d’entrées. Ensuite, une approche par régression linéaire du second degré a été choisie pour initier le modèle d’apprentissage. Suite à la validation statistique du modèle sur un jeu de données, INOVSYS a développé une boucle d’optimisation des paramètres. Une approche par gradient dite « hill climbing », ainsi qu’une approche aléatoire dite « random search » ont permis la prédiction de paramètres d’entrée optimisés parmi ceux évalués.
Puis, de nouvelles éprouvettes fabriquées selon ces paramètres optimaux ont été imprimées afin de valider la pertinence du modèle.
Les essais réalisés sur ces éprouvettes ont confirmé une amélioration significative des propriétés mécaniques, de l’ordre de 10%, proche de la prédiction du modèle.
Compte tenu de ces résultats encourageants, INOVSYS poursuit ses travaux en augmentant le nombre de paramètres testés et le nombre d’éprouvettes imprimées. Cela permettra d’affiner le modèle de prédiction et d’exploiter encore plus tout le potentiel du Machine Learning dans la compréhension des procédés de fabrication additive et l’optimisation des pièces industrielles de demain.
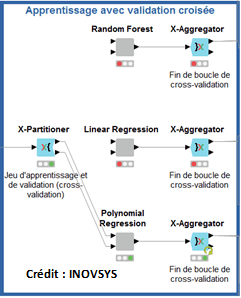
En parallèle de ces travaux, INOVSYS a démarré un projet de R&D collaborative visant à développer des fils chargés, autre solution à la réalisation de pièces à hautes performances.
Contactez notre équipe pour plus d’informations sur la prise en main de vos matériaux complexes.
Apprenez en plus sur le procédé FDM et sur les bonnes pratiques à mettre en place via nos articles dédiés et nos formations personnalisées à vos besoins.
Découvrez nos actualités